Navigation:
Office & Hotels · Factories · What is an EC fan?
Heating, ventilation, and air-conditioning (HVAC) applications account for a significant portion of energy use in commercial buildings. In hot and humid countries, like Singapore, it can account for up to 50% (NCCS, 2011). Therefore, to reduce the energy consumption of buildings, implementing green technology for HVAC applications is a strategic move.
Fans are among the HVAC application components that consume a considerable amount of energy (NCCS, 2011). Among the available fan types, EC fans are far more energy-efficient compared to their conventional AC counterparts. Hence, by using or retrofitting EC fans in HVAC applications, the energy consumption of buildings can be reduced significantly.
Discover EC fan solutions for office and hotels
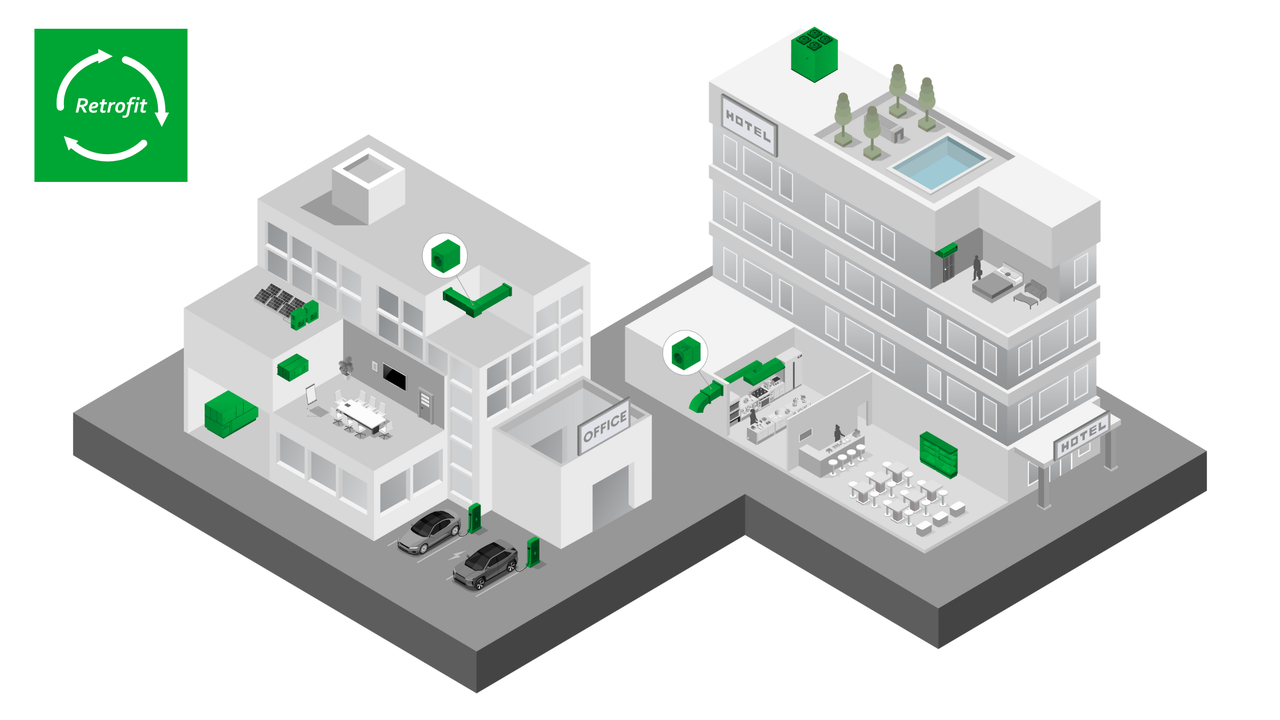

Retrofit
Discover our retrofit solutions for HVAC applications at a glance!
Learn More
Air Handling Unit
Discover the EC fans that are ideal for air handling units and why!
Learn more
Cooling Tower
Discover the EC fans that are ideal for cooling tower units and why!
Learn more
Large Fan Coil Unit
Discover the EC fans that are ideal for large fan coil units and why!
Learn more
Small Fan Coil Unit
Discover the EC fans that are ideal for small fan coil units and why!
Learn moreOffice and hotel buildings receive a large amount of human traffic. The HVAC applications within these buildings need to run smoothly in order to ensure the occupants’ comfort levels. In some cases, HVAC applications may be required to run 24/7. For example, as the hotel lobby operates day and night, it will require air-conditioning or ventilation at all times.
HVAC applications also serve other functions, such as expelling unwanted and unclean air in restaurants and ensuring that perishable goods are kept cool. EC fans can bring incredible value to these applications by reducing the overall energy consumption needed to keep HVAC applications running. This is beneficial for both the building owners and the environment alike.