In which direction is drive engineering developing? Johannes Moosmann: For some time now we've been experiencing an increasing trend toward decentralization. Before, you had large motors with vertical shafts but today, applications are being fitted with drives that are increasingly more compact. A new development is that Industry 4.0 is moving away from the conventional automation pyramid: all of the components communicate with one another and, as a result, generate a connectivity network that spans from the main computer to the actuator/sensor level. In other words, the industry is trending toward small motors with integrated electronics. And what type of requirements do the drives need to fulfill? Drives can have a multitude of different uses across various sectors. As a result, the particular requirements in terms of performance, structure, control characteristics, and energy efficiency are also very different. This means that we're expected to offer a high degree of variety, but at the same time customers also want solutions to be cost-efficient, of course. However, variety often gets in the way of cost efficiency. How do you solve this contradiction at ebm-papst? A main solution to this – partly contradictory – customer requirement is our modular system, which provides customers with a number of advantages: faster volume deliveries, more cost-efficient solutions, a high level of quality, and faster specifications. The customer tells us their requirements and we compile a drive solution from our modular system that fulfills these requirements in the best possible way. This enables us to circumvent the otherwise lengthy development phase typical of a specific product. But what happens in instances when the modular system can't meet 100 percent of the requirements? The modular system offers a vast range of potential motor, electronics, and transmission solutions. Usually, once the modular solution has been implemented, the customer can continue using their application. We also differentiate between standard and preferred types, whereby the latter are ready to be dispatched within 48 hours. This means that the customer can test the product in their application quickly. In the meantime, we can dedicate our full attention on the final part of the solution, so it meets 100 percent of the requirements. The modular system contains pre-developed and pre-qualified individual modules, which enables us to significantly speed up the development phase. The pre-qualified modules also ensure that the entire product will work without fail. Doesn't the vast range of the modular system complicate the customer's decision-making process? On the contrary: our answer to complex customer requirements is integrated solutions comprising motors, electronics, and transmissions, which – depending on the requirements – are compiled from our modular drive system. This is combined with a consultation service that provides a high degree of technical expertise. How does your support system work exactly? Well, we have an online portal, for example, where you can make your initial selection. It not only lists technical performance characteristics, customers can also download 2D drawings and 3D models of the drives, making it very easy for customers to integrate them. What role does the individual consultation service play? As before, this is still a very important element. It's within our ebm-papst genes to deliver precisely the level of service needed by each individual customer. We go to the customer, try to understand the application, and together devise the drive system specifically needed to solve their exact drive task. We have drive experts assigned for this very purpose, who are at the customer's disposal with specialist and business expertise. At the moment we're working on the global expansion of our team of drive experts. As our drive experts are technicians through and through, they can converse on the same level with the customer's development team. In general, a customer's core competency is in understanding the application, not the drive – and this is what they should still be able to focus on. Another ebm-papst gene is energy efficiency. What is the potential for improvement in this area? As we take the entire drive system into account, we're able to design it in a very efficient manner. Our ongoing transmission development process ensures smooth operation and the highest levels of efficiency. Our motor and control expertise in St. Georgen plays a key part in this. The combination of motor and electronics alone produces an efficiency level of up to 95 percent. Of course, from a purely technical perspective we could offer even more efficient drives – but this would increase costs. We would rather offer our customers high-efficiency products at more economical rates. One of the market requirements is to build drives as small as possible... Our BLDC motors are incredibly compact and powerful compared with AC and brush motors. This means that the drives can be installed directly into the customer's application, which in turn supports our modularization approach and improves precision, product safety, and therefore availability. In line with the trend of battery-powered solutions, these motors are also advantageously lightweight. In the examples you mentioned, connectivity also plays a huge role. What solutions can you offer in this regard? If required, our drives also come with integrated intelligence. The motor doesn't just record and report its own statuses, it can also be used as a basis for analyses, for example, to identify malfunctions within the application. This means that our compact drives are ideally suited to aspects such as condition monitoring and predictive maintenance. What are the future possibilities in this area? We'll be able to give customers access to a lot of data. Sensors in the motor record a lot of parameters, which can be exported in real-time. We can also calculate statuses using the integrated intelligence of the drives. In future we'll also be able to report on position, temperature, speed, torque, and current values, helping the customer to improve their understanding and optimization of the entire system. A more simple installation process via a self-learning system is also a possibility, whereby the motor starts up and determines the optimum control parameters by itself. For which bus system have the drives been designed? Unfortunately, in the field of drive engineering there isn't a focus on a specific bus system, but rather on a large range of different systems. At the moment we offer drive systems with the CANOpen protocol and in future, we'll be able to offer other commercial bus systems. Profile of Johannes Moosmann Johannes Moosmann studied mechatronics in Ulm and later went on to complete an MBA. He has been employed at ebm-papst in St. Georgen since 2003. He was initially responsible for Process and Production Development and appointed as Assistant to the Director for Organizational Development. In 2011, he became Director of the Industrial Drive Engineering business unit.
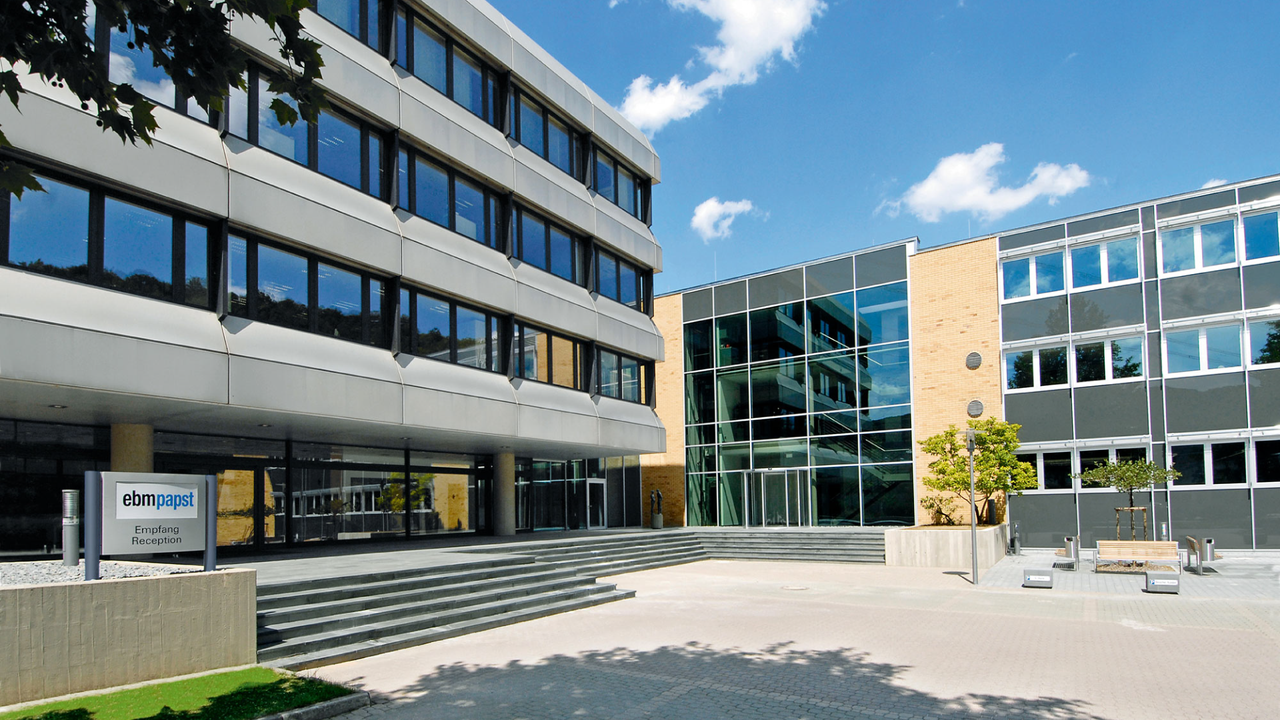